Table of contents
The electronics industry produces all sorts of products that we rely on every day, but it is also responsible for its fair share of environmental degradation and pollution. Things have gotten better ever since the beginning of the Pb-free movement, to the point where it is broadly accepted that the use of Pb-free components is the norm and not the exception. This movement as well as the environmental movement more generally also brought us REACH and RoHS, two European directives which have had global influence on sourcing and production decisions.
Now the industry is being directed to confront a new set of hazardous substances that present long-term health effects to humans due to their persistence in the natural environment. These are per- and polyfluoroalkyl substances, or PFAS. These substances can be found in many materials and components in an electronics assembly, and the semiconductor industry uses some of these substances to manufacture components. With regulatory attention being given to these substances, who is responsible for their limitation and how can buyers ensure product compliance?
Why PFAS Are Being Limited
PFAS refers to a group of 4730 man-made chemicals that persist in the natural environment. Their chemical properties are based around the presence of carbon-fluorine bonds, which are the strongest bonds found in organic chemistry. This makes PFAS very useful in manufacturing electronic components and assemblies, but it makes these chemicals degrade very slowly through natural processes. This causes these compounds to persist in a variety of finished products, resulting in human exposure.
If these chemicals were not toxic to humans or the environment generally, probably no one would care about their presence in electronics or in other products. However, these substances are known to contribute to long-term human health problems, including thyroid disruption, immune system disruption, liver damage, and cancer.
PFAS are contained in many components and materials used in electronic devices, including but not limited to:
- Cable and wire sheathing
- Laminate materials for PCBs
- Passive components
- Displays (such as LCD displays)
- Batteries
- Packaging materials
- Enclosure materials
As a result, two US states (Maine and California), the US Environmental Protection Agency, and the European Chemicals Agency have enacted rules or new regulations regarding the presence of PFAS in products released to market. These actions do not eliminate or prohibit the use of PFAS in electronics, but the end goal is to reduce the potential for consumers to be exposed to these substances.
PFAS Adds New Compliance Dimensions
Ensuring compliance with PFAS-limiting regulations and directives falls on the shoulders of two groups:
- Component manufacturers and materials manufacturers
- Designers and manufacturers, who select and use materials and components
Currently, manufacturers of components and materials will have the greatest responsibility to ensure their products do not contain excessive levels of PFAS. Materials manufacturers, especially PCB materials companies, already have a big hurdle to overcome. Currently, over 90% of FR4 laminate materials used in PCBAs include PFAS substances, so laminate manufacturers will need substitute materials that can help ensure compliance with PFAS limits.
How PFAS limitation will be indicated on products so that designers and manufacturers can ensure compliance is another matter. Currently, many manufacturers offer RoHS/REACH and Pb-free compliance guarantees, both at volume and in prototyping. Even small manufacturers offer RoHS-compliant production options and Pb-free assembly offers on their quote forms. Manufacturers who produce chemicals and materials needed for PCBA production (cleaners, solders, fluxes, etc.) also indicate compliance on their product labels.
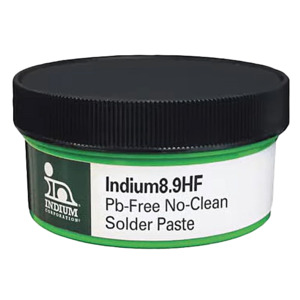
PCBA manufacturers will soon play an important role as they compile data on PFAS content in products that leave their factories. Currently, it is difficult for every company to guarantee PFAS limit compliance without testing every assembly and cataloging these data internally. Their compliance dimensions involve the use of compliant supplies from their vendors, as well as qualification of their processes against requirements in PFAS regulations.
Obviously, PCB designers and product engineers don’t have time to purchase and chemically test every single component they intend to include in an assembly. Therefore, it will most likely fall on manufacturers to provide some sort of compliance indication. Currently, for RoHS compliance and Pb content, this information can be found in a component datasheet, as shown in the example below.
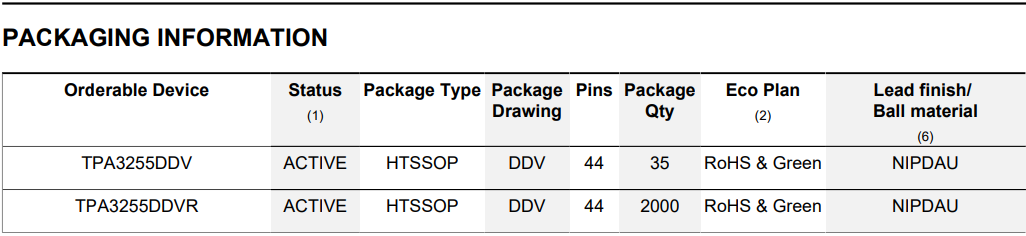
In conclusion, don’t be surprised if you start to see some kind of PFAS compliance label on products and components in the near future. Supply chain management and component information systems will also need to start indicating this information to users so that they can quickly identify the products they need to remain compliant with these regulations.
Cofactr gives electronic component buyers instant visibility into component information and important compliance for their electronic parts, including REACH and RoHS. Electronic design teams and procurement professionals use Cofactr to quote, purchase, manage inventory, and manage logistics for their electronic components. Cofactr also provides warehousing and logistics management services through its online platform.