Table of contents
Whether you need to ship or receive packaged components or assemblies, your parts or boards will need to be packaged in the right materials for storage or shipping. Many packaging materials for shipping double as storage materials, so it pays to keep both on hand. If you’re an assembler or you have an in-house assembly team, the parts you receive should come in the right packaging.
Depending on where parts are procured, parts may not always come packaged properly. Incorrect packaging is telltale sign of a reworked part, used part, or possibly even a counterfeit part. In some cases, a distributor has authentic parts but simply neglected to repackage components properly. Similarly, when you ship out completed assemblies, you should make sure you use the correct packaging for your components and PCBAs.
Here’s an overview of the packaging materials your company should keep in stock and what packaging materials you should expect from your component vendors.
Packaging Materials for Parts and Assemblies
Component Packaging
Electronic components have various packing requirements that are intended to protect parts from the environment, from mechanical damage, and from electrical damage (e.g., from ESD). The typical component packaging materials used to pack and ship components must meet some simple requirements:
- Provide protection from ESD (typical 2 kV or higher)
- Provide protection from dust and moisture
- Withstand contact with other chemicals, such as solvents
- Prevent loss of components during transport and handling
To meet these requirements, typical packaging materials include antistatic bags, antistatic packing materials and bubble wrap, antistatic plastic baggies, and vacuum-sealable versions of these items. These can be purchased from most industrial supply companies.
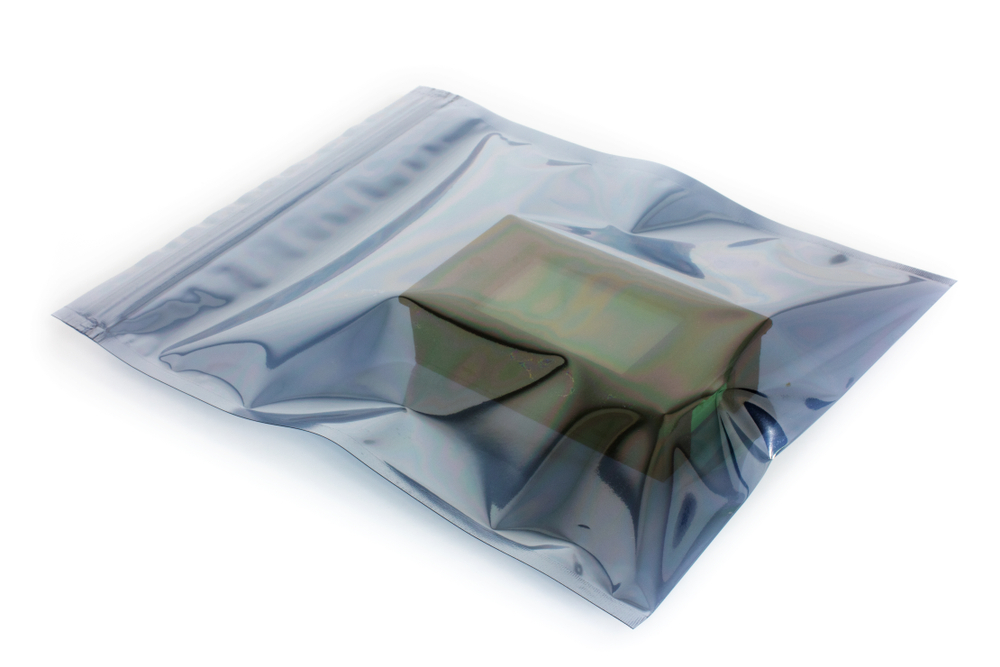
Some components require additional environmental protection, specifically from moisture. Moisture sensitivity level (MSL) ratings on components will dictate the level of humidity and packing procedures that will be required for components and finished assemblies that contain certain moisture sensitive components.
Moisture Protection
Moisture-sensitive components require packaging that acts as a reliable moisture barrier while also protecting the electronics from ESD. When you order a batch of components, make sure you understand the moisture sensitivity rating of the components. Packaging for moisture-sensitive components might be difficult to distinguish from standard electrostatic safe packaging just by sight. You can typically spot moisture-safe packaging from a few characteristics:
- The packaging might state “moisture safe” or something similar on the outside
- You should be able to feel desiccant bags through the packaging
- The packaging is often vacuum-sealed
- There may be a moisture indicator card inside the packaging
Moisture-sensitive components are also described as such in their datasheets. Currently, the J-STD-020 standard (revision F) specifies a total of 8 MSL ratings for electronic components. These ratings provide the maximum permissible exposure for electronic components once they are exposed to humid air before they require baking to remove moisture. The 8 MSL ratings are summarized below; learn more about MSL ratings for electronic components.
- MSL 1: Lowest sensitivity rating; unlimited floor life.
- MSL 2: Maximum safe exposure of 1 year.
- MSL 2A: Maximum safe exposure of 4 weeks.
- MSL 3: Maximum safe exposure of 168 hours.
- MSL 4: Maximum safe exposure of 72 hours.
- MSL 5: Maximum safe exposure of 48 hours.
- MSL 5A: Maximum safe exposure of 24 hours.
- MSL 6: Mandatory baking before use.
If you’re working with a 3PL to store, ship, and track parts orders, then it’s very important that you receive MSL reset notices for parts in your BOMs. An MSL reset notifies a customer that their parts need to be baked to reset their safe exposure time before the parts are used in assembly. Not all 3PLs offer this level of service, and component distributors certainly don’t provide these notices to customers.
PCBA Packaging
PCBA packaging can involve all of the above packaging materials for components, which is to be expected as you are basically shipping a batch of components plus a PCB. A PCB with moisture sensitive components should be packaged in the same kind of moisture barrier packaging, including desiccant and a moisture indicator. Vacuum packaging may also be needed in these assemblies. In some cases, a conformal coating should be used to help protect the device from the environment.
Environmental protection won’t provide any mechanical protection. Therefore, the assembly should be packaged in some protective shipping material. Usually, this will be antistatic bubble wrap, or an antistatic padded box could be used for larger assemblies.
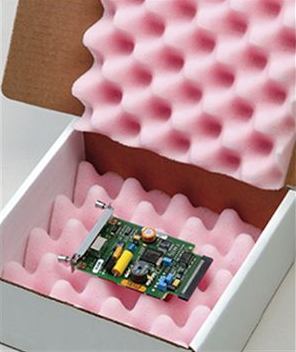
Another safety measure for larger components and finished assemblies is to use antistatic bubble wrap. This provides an extra layer of protection during shipping and while handling an assembly. If you’re unsure of everything you need to use to pack, ship, and store components properly, watch how authorized distributors handle parts, or contact semiconductor vendors for assistance.
Watch Out For Correct Packaging
For the most part, authorized distributors will only use correct packaging that follows the guidelines direct from parts manufacturers. Although authorized distributors are essentially repacking components when they kit parts for your order, they are highly experienced in this area.
One tricky area is in dealing with parts resellers and brokers. It’s possible these dealers will not use correct packaging, or they may reuse old packaging that does not provide the required level of environmental protection. This puts your components at risk for contamination or exposure to the environment. If you opt to work with a 3PL to manage all of this, make sure your 3PL provides testing, inspection, packaging, and kitting services so that these issues can be identified and corrected before assembly.
If you want to reduce your component risk and simplify your procurement processes, you need an ITAR-compliant platform like Cofactr. Electronic design teams and procurement professionals use Cofactr to quote, purchase, manage inventory, and manage logistics for their electronic components. Cofactr also provides testing, inspection, warehousing, and logistics management services through its online platform.